A distributor rotates at half the crankshaft speed (in four stroke applications, same speed as the crankshaft in rotary and 2 stroke applications) and routes the high voltage generated by the coil to the intended spark plug via a rotor and HT wiring. A standard distributed engine requires one ignition drive and a single channel igniter, rotary engines and twin distributer engines require two coils. On a single coil distributed engine Ignition Drive 1 is used to switch the igniter.
Because the rotor will only point to each post on the distributor cap for a short amount of time, the rotor timing dictates the range of ignition advance angles that may be used without misfiring or unnecessarily losing spark energy. A wider tip on the rotor will also allow a wider range of timing values to be used. The tip of rotor should be just leaving the post when the crankshaft is positioned at the minimum timing that will be used (typically at about 10 degrees BTDC). The point where the leading tip of the rotor arrives at the post is the most advanced timing that should be used.
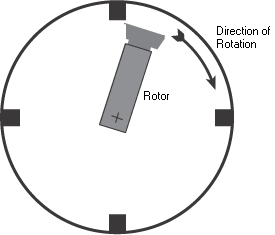
Correct Rotor Timing