The following procedure outlines the essential steps that must be performed for a working Electronic Throttle Control installation.
WARNING: Electronic Throttle Control is an advanced feature and should only be used by an experienced installer and tuner. DO NOT attempt to configure any part of the Electronic Throttle Control system if you are at all unsure or do not have sufficient experience to do so.
At any time, faults or problems will be displayed as ECU fault codes. These will appear in the top status bar in PCLink and also in the ECU Status runtime values. As these fault codes are permanently stored, the clear fault codes procedure must be followed after each fault code has been dealt with. Click HERE for information on clearing ECU fault codes.
1.Wiring - All Electronic Throttle Control hardware must be correctly installed and wired as per the diagrams found in the ECUs Wiring and Installation Manual.
2.Before Power Up - Remove the Electronic Throttle power supply isolating relay (or external controller power supply) before first powering up the new installation to prevent any chance of power being unexpectedly applied to the actuator.
3.Enable Electronic Throttle Control - In PCLink, set the Electronic Throttle Control Mode to 'Setup Mode'.
4.Set PWM Output and EThrottle Relay to the outputs that they have been wired up to
5.Setup the rest of the E-Throttle Setup window including setting appropriate DC clamp values.
6.Setup the Target Table - The target table should be configured to give the desired throttle plate vs accelerator position movement.
7.In the Accelerator Position Sensor window set the APS (Main) and APS (Sub) Source settings
8.Set the rest of the APS settings and calibrate it either manually or using the APS Calibration function.
9.In the Throttle Position Sensor window set the TPS (Main) and TPS (Sub) Source settings
10.Set the rest of the TPS settings, at this point the TPS can be calibrated manually, to calibrate it using the automatic TPS Calibration function a few more steps will need to be done first.
11.Connect Power - Install the isolating relay (connect power to the external controller). Watch and listen in case the throttle plate snaps open unexpectedly.
12.At this point the TPS Calibration function can be used, first ensure the throttle body is clear of any objects. If the calibration states that the H Bridge Polarity is reversed this can be rectified by changing the Active State of the first Aux that is being used for the PWM Output (Aux 9 when using Aux9/10).
13.Setup the Control Algorithm - Tune the throttle plate control algorithm if required.
14.Test Electronic Throttle Control - In PCLink, set the E-throttle Mode to ON. Clear ECU Fault Codes and check no fault codes return and that the throttle plate is being controlled correctly.
WARNING: The electronic throttle mode 'Setup Mode' is provided only for configuring the system with the engine not running - all safety features are disabled. The vehicle MUST NOT be driven in 'Setup Mode'.
Most Settings can only be configured when E-Throttle mode is set to Setup Mode or Disabled mode.
·OFF - Electronic Throttle Control is turned off.
·ON - Electronic Throttle Control is turned on and has all safety features enabled.
·Setup Mode - Electronic Throttle Control is turned on and has all safety features disabled. This Mode must only be used for configuring the System, the vehicle MUST NOT be driven in this mode.
·Disabled - Electronic Throttle Control is turned off but the tables remain allocated and all settings remain visible.
Allows the user to select which pair of output pins will be used to control the EThrottle motor, Aux1/2 & Aux3/4 require an External Ethrottle Controller whereas Aux9/10 has a built in controller and can be connected directly to the EThrottle motor.
The Active State of the first Auxiliary in the selected pair can be used to change the direction that the H-Bridge drives the EThrottle.
Allows the user to select which output pin will control the EThrottle Power Relay. The Ethrottle power relay controls whether or not power is supplied to the Ethrottle controller and so is an essential part of the built-in safety features. Refer to Generic Internal E-Throttle Wiring for an example of the Ethrottle Relay wiring. External Ethrottle Controllers often have a built-in Relay in which case the Ethrottle Relay output pin should be connected to the appropriate pin on the controller.
For Toyota and Lexus E-throttle systems that have a clutch in the throttle body, wire the clutch ground to an Auxiliary Output and either set the 'E-throttle Relay' to that auxiliary output or set the output Test (PWM) on and set the frequency to 250 Hz.
Allows the user to set the frequency of the PWM Output Signals, typically a value of 500Hz-1kHz is appropriate. If using an external Ethrottle Controller the frequency will be determined by that controller not the ECU and so this setting will have no effect.
Gain with respect to the difference between actual value and target value. (Typically around 7.00, must be checked).
Gain with respect to the accumulated offset between actual value and target value. (Typically around 0.145, must be checked).
Gain with respect to the change in difference between actual value and target value. (Typically around 25.00, must be checked).
Maximum % duty cycle that will be applied to the motor driver. (Typically around 90%, must be checked).
Minimum % duty cycle that will be applied to the motor driver. (Typically around -90%, must be checked.
·Run Throttle - Throttle is controlled as per normal when engine speed is 0rpm.
·Quiet Throttle - Throttle Control will not operate when engine speed is 0rpm.
Allows the user to set how long a fault condition must be active for before a fault occurs. The default value is 1s.
The E-Throttle Target Table provides a means by which the amount of throttle can be set.
One axis on the E-Throttle Target Table would typically be set to AP(Main), usually the Y axis. The other axis is typically set to Engine Speed but could be any relevant parameter.
The value entered into the table represents the target position for the throttle plate. Numbers can range from 0% (fully closed) to 100% (fully open).
It is recommended on initial setup to set the table for a 1 to 1 ratio. This can be done by setting all the target numbers to match the corresponding AP(Main) row or column number. More advanced tables can be generated to provide more or less throttle plate to accelerator position ratios. For example, a race situation may see high target numbers at areas of low accelerator position whereas a road application may have less throttle opening than the actual accelerator position to improve economy.
The following table gives an example of a typical full throttle table setup.
Notice some of the key features:
·It is recommended to use a 0% throttle target value at 0% APS when using Ethrottle idle control as the G4X idle software is set up to provide a smooth and responsive entry and exit from idle which means any EThrottle target greater than 0 will increase the actual idle position.
·A column of low throttle angles at 7200RPM to help limit the engine speed. (You may not want this in turbo charged applications as it can create turbo-lag).
·The accelerator to throttle ratio is not 1:1 but has been setup to give the driver greater control of low throttle angles.
Note that the first column of the table being 7000rpm means anything up to and including 7000rpm will use those values and anything between 7000 and 7200 rpm will be interpolated.
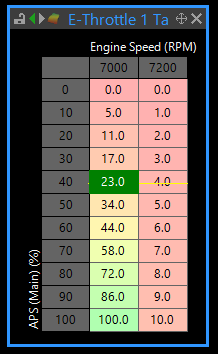
Example Full Table
Note: Only EThrottle 1 supports multiple target tables.
You can setup three different target tables and switch which table is currently active by selecting an appropriate DI/Aux etc and can use GP Outputs to further customise your switching options.
The setup of multiple tables is completed through the following settings:
Sets the number of target tables used.
Sets the activation method for E-Throttle Target Table 2. This table has priority over E-Throttle Target Table 1 only.
Sets the activation method for E-Throttle Target Table 3. This table has priority over E-Throttle Target Table 1 and E-Throttle Target Table 2.
Application Example
You may want to create two different target tables, each providing a completely different throttle feel.
·Set E-Throttle Target Table 1 up as a "Street" table, this table could potentially limit the maximum throttle angle and provide more precision control over low throttle angles.
·Set E-Throttle Target Table 2 up as a "Sports" table, this table would allow maximum throttle angle and provide more precision control over large throttle angles.
To implement this:
1.Set Active Tables to 2 Tables.
2.Set Table 2 Activation to the appropriate DI channel connected to the selection switch.
3.Configure E-Throttle Target Table 1 and E-Throttle Target Table 2 as required.
4.Use the switch to toggle between tables.